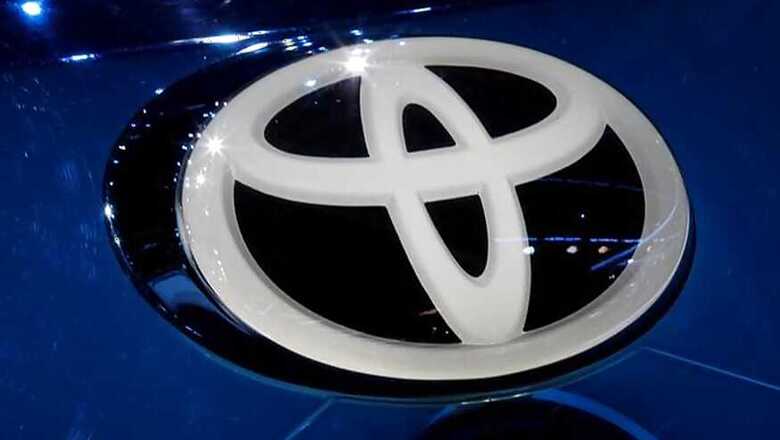
views
Over the last one decade, plastic pollution has become a worldwide phenomenon and its ramifications in terms of waste management have become a critical issue that the world is facing today; both from the perspective of resource availability and its impact on our eco-system. Reports on waste management by the World Bank suggest that by 2050, the world is expected to generate 3.40 billion tons of waste annually, increasing drastically from today’s 2.01 billion tons. While the East-Asia and Pacific region are likely to generate close to a quarter (23 per cent approx.) of all the waste and South Asia will more than double its waste stream.
Toyota announced the “Toyota Environment Challenge 2050”, a one-of-its-kind long-term initiative aiming to minimize carbon dioxide emissions and have a positive impact on the environment. As part of the six challenges to be achieved by 2050, Toyota has taken upon itself to establish a recycling-based society and systems, inspired by its philosophy of Toyota Earth Charter, which encourages pursuing production activities that do not generate waste.
Aligning its activities with the Toyota Environment Challenge 2050, TKM established a robust waste management system at its operating facility at Bidadi, in Karnataka. Its five-year action plan derived from the Toyota Earth Charter is also in place which speaks on “Reduction in Hazardous Waste Generation” and “Continuous Efforts to achieve Zero Waste to Landfill”, giving the reduction targets. With these efforts, TKM is ensuring zero waste directly to landfill and achieved recyclability of 96 per cent to date, for the wastes which are generated from the manufacturing operations.
Commenting on the initiatives taken by TKM, Masakazu Yoshimura, Managing Director, Toyota Kirloskar Motor said, “Keeping in-line with our global Toyota Environment Challenge 2050 and aligned with the honorable Prime Minister’s nationwide campaign to limit the consumption of single-use plastic, we have proactively implemented several initiatives encouraging our stakeholders to reduce, recycle and reuse, as a step towards a better tomorrow.” He further added, “Environment consciousness is etched into Toyota’s ecosystem, right from our supply chain to our management and employees to the beneficiaries on the ground ensuring a sustainable impact. Through this initiative, we are committed to building a sustainable waste management system to reduce the negative impact of single-use plastic.”
As part of the project, TKM also conducted an extensive study to find alternative options for waste minimization to utilize biodegradable waste (non-Hazardous) in an eco-friendly manner. The study involved testing various composting techniques, and the team arrived at ‘vermicomposting’, a process of composting using various worms, usually red wigglers to create a heterogeneous mixture of decomposing waste. As a result, with the use of this technique, of the 6 MT of bio-sludge generated at the plant, 4 MT was converted to manure (fertilizer). This helped in reducing the landfilling cost up to 28.8 lakh per annum and also curtailed the emissions up to 18 tCO2e/annum.
Understanding the extent of issues of the plastic wastes and global drive for the establishing the circular economy, in 2018, TKM accelerated its efforts towards reducing the plastic waste and started a company-wide drive ‘5R’. With its well-defined strategy for identification of the Kaizen’s (continuous improvement), TKM promoted the reduction activities involving its employees. Various activities taken up as part of the 5R initiative yielded a reduction of 45% in plastic footprint over the period of June 2018 till June 2019.
The company has also implemented the elimination of plastic in Service Parts Operation. Thorough studies are being conducted to stop plastic usage and introduce alternate material like paper and cotton bags for primary & secondary packaging, strapping etc. Overall implementation of the campaign to ban plastic usage/ introduction of alternate packaging material across suppliers will start by January 2020.
With the auto industry going through a dynamic revolution, End-of-Life Vehicle Management is proving to be one of the biggest challenges in the coming decades. TKM conducted a detailed study of the existing dismantling markets in India, only to realise that the prevailing informal sector can pose a severe threat to the environment. A car is an assembly of more than 800 parts and can be dangerous to the environment if disposed of unscientifically. Considering this issue, Toyota Motor Corporation devised a program called the 100 dismantler project, where Toyota is developing 100 model dismantling facilities around the world to promote material recycling of the end-of-life vehicles.
Guided by the Challenge 2050, TKM has also developed an "EcoZone" in its premises at Bidadi. It is an outdoor environmental learning centre, specially designed to provide experiential learning to stakeholders. Under this project, TKM aims to connect "Children with Nature", promote environmental awareness beyond classroom learning and inculcate a behaviour towards the conservation of our environment. So far more than 1900 students from 52 schools and colleges have been a part of this training at the Ecozone.
Further, Ecozone also houses the Value Theme Park dedicated to educating the stakeholders on the importance of waste management, solutions for effective value creation from waste and ways to move towards a Zero Waste Society. The theme park highlights the key issues of waste management in the society and industry and provides a platform for triggering discussions to evolve solutions.
Comments
0 comment