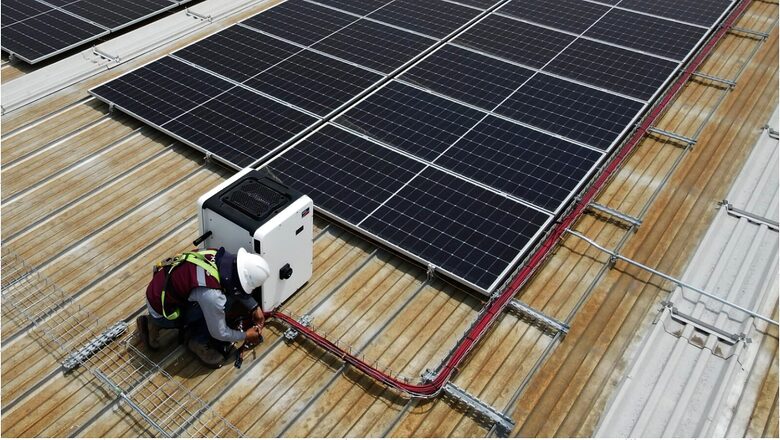
views
As the world looks for cleaner power, discussions over solar energy and its viability have increased dramatically in the last five years, with experts calling it the best sustainable choice, but some have pointed out it not being eco-friendly enough.
According to the International Energy Agency, photovoltaic (PV) cell or solar cell, capacity has increased from 1.4 GW in 2000 to 760 GW in 2020 globally and solar energy now produces close to 4% of the world’s electricity.
But there are some issues related to the materials used to make solar panels and the manufacturing process, which is quite energy-intensive.
As some experts consider these highlights as challenges related to the solar energy sector, News18 spoke to industry insiders to understand their points of view on such crucial matters.
Manufacturing
While talking about the manufacturing process Ankit Singhania, Director (Sales & Procurement), Navitas Solar said “it depends on technologies”, as manufacturers having the same technology follow the same process, but quality standards and inspection points are quite different.
Shubhra Mohanka, Director in Gautam Solar, said: “Some manufacturers follow the manual process for solar panels manufacturing and others like ourselves follow the automated process, adopt the latest machine technology and do innovations from time to time to make the same modules.”
Meanwhile, Raman Bhatia, Founder and Managing Director, Servotech Power Systems Ltd, said certain manufacturers are quite objective “while a few approaches followed might differ from one manufacturer to the other”.
The majority of solar PV modules typically include solar cells, glass, EVA, a back-sheet, and a frame as their standard parts. Additionally, there are three main types of solar panels on the market and these are thin film, monocrystalline, and polycrystalline.
As a result, according to Bhatia, there are several materials available for manufacturers at the level of the cell structure, including mono silicon, polysilicon, cadmium telluride (CdTe), copper indium gallium diselenide (CIGS), and amorphous silicon (AnSi).
“The first two types of cells are produced using a methodology that is somewhat similar. Testing is done when the module is finished to make sure the cells function as planned. Here, the Standard Test Conditions (STC) are utilised as a benchmark,” the industry insider noted.
While sharing more details about the solar panel manufacturing, he said all manufacturers use NOCT (nominal operating cell temperature), which measures the performance of the panel against real-world factors such as the module’s operating temperature at 800W/m2 of solar radiation, 20°C of ambient temperature, and 1m/s of wind speed.
However, solar panels are primarily made of silicon, which requires a lot of heat to shape it properly, and, as a result, the solar panel manufacturing process does emit some CO2. So, the question is whether the process should be classified as an “unclean” source of energy.
In that case, Mohanka said there might be some potential impact on the environment associated with the manufacturing of solar panels. However, the most important thing to remember is that solar power significantly reduces the hazardous environmental impacts caused by emissions from fossil fuel-based power generation.
“Solar power generation involves low air emissions of air pollutants such as sulphur dioxide, nitrogen oxides, carbon monoxide, volatile organic compounds, and the greenhouse gas carbon dioxide,” she added.
Additionally, Gautam Solar’s director also said significant players in the sector are currently working on the innovation of cutting-edge technologies to take care of the destructive environmental issues related to solar manufacturing.
Bhatia said there is a lot to optimise when it comes to producing photovoltaic panels such as carbon emissions, hazardous waste, unsustainable mining methods and more. “But it’s crucial to keep in mind that solar panel design isn’t constant… Additionally, as the use of renewable energy increases, the manufacturing process will get cleaner,” he noted.
Health Issues
Did you know that quartz sand or silica sand is essential for producing solar panels? But this material is associated with health issues and workers who inhale tiny crystalline silica particles are more likely to develop serious silica-related diseases such as silicosis, lung cancer and chronic obstructive pulmonary disease (COPD).
Navitas Solar’s Singhania said this pollution is associated with cell manufacturing but Bhatia said he believes with the solar industry evolving, this issue will be resolved. Bhatia said prior to drilling quartz, sand mine operators usually remove overburden, which also lessens the amount of fine material that can become airborne by blasting. So, if needed during summer periods, water may also be sprayed onto blast areas to minimise fugitive dust emissions.
While agreeing with the fact that the quartz sand carries certain health issues and that production of the solar panels might involve toxic chemicals, Mohanka said the solar manufacturers and the government have been proactive in addressing the issue. “It needs to be ensured that primarily solar panels are manufactured from thinly cut wafers of crystalline silicon produced by metallurgical silica. In line with this, the solar manufacturers are increasing the use of High Purity Quartz Sand (HPQS), and making the silica use for PV panels at least 99.99999% pure,” she noted.
Environmental Effect
It is noteworthy that the chemical reaction that creates polysilicon produces a by-product called silicon tetrachloride. If it is not disposed of properly, it can cause soil acidification and emit harmful fumes.
Though the recycling of silicon tetrachloride back into polysilicon and reusing it in the production of more solar panels is found by the experts, the process is still needs improvement.
Bhatia said the safe handling, storage, and disposal of chemicals and waste pose big challenges to the state of the solar industry today. “We can limit the quantity of waste produced and increase chemical handling safety by taking a few specific actions.”
Additionally, Bhatia said: “This entails clearly labelling and organising all chemicals, keeping them all in one place, designating hazardous chemicals as “hazardous,” establishing standard operating procedures (SOPs) for every process that calls for the handling of hazardous chemicals, and properly disposing of hazardous waste in containers that are clearly marked.”
Dumping Solar Panels
PV panels have a lifespan of about 30 years, and recycling technologies for these units are inefficient and rarely used. These also contain toxic materials that can pollute the environment, yet many are discarded in landfills.
What makes it more concerning is the fact that, according to projections, 8 million metric tonnes of these panels will have reached the end of their useful lives by 2030, with the total expected to reach 80 million tonnes by 2050.
Singhania said to ensure environmental safety plastic material, back sheet, Eva, and cells should be removed separately, while from solar cells, copper and silver can be extracted and glass can be recovered and recycled.
Meanwhile, Servotech Power’s Bhatia said to successfully recycle a silicon module, project owners and manufacturers should focus on removing the 100% reusable aluminium frame, separating glass along a conveyor belt (95% reusable), processing thermally at 500 degrees Celsius, allowing small plastic parts to evaporate, making it simpler to separate the cells and melting into silicon wafers reusable slabs (85% recyclable).
Mohanka said: “To sustainably leverage solar energy, there is a need for a circular solar economy through which the wastes from solar cells and modules can both be diverted and reused as valuable sources for new solar modules.”
The Road Ahead
Here it should be noted that recently the Union cabinet approved the second tranche of the Performance Linked Incentive scheme to boost the manufacturing of PV modules in India.
When asked whether India needs a dedicated policy or regulations focusing on this sector, Navitas Solar’s Singhania said, “We should have some regulations and policies from the government on solar panel recycling.”
Mohanka from Gautam Solar said in its endeavour to install 450 GW of renewable energy by 2030, which includes 280 GW of solar power, the government has already been taking proactive measures to provide capital subsidies, tax breaks, along with cheaper land parcels near ports to be developed as manufacturing hubs to facilitate export opportunities.
India’s Solar Future
Mohanka believes that to bring in a green revolution in the country, industry players in the solar energy sector should invest more time and money in indigenous innovations and self-reliance and increase domestic production at a fast pace
“India needs to take some immediate measures in the next five years like consistent regulations for net metering and banking facilities, restrictions on banking revoked at least until rooftop targets have been achieved, strict enforcement of the renewable purchase obligation (RPO) by states, and capital subsidy for battery energy storage systems (BESS),” Mohanka added.
Singhania from Navitas said among all renewables, solar is the most preferred one as it has less maintenance and India is a country to have an ample amount of solar irradiation throughout the year.
Servotech’s founder Bhatia said solar PV electricity may be efficiently used, offering enormous scalability as well as enabling power to be generated on a distributed basis with quick capacity additions.
He suggested: “From the perspective of rural electrification and satisfying other energy needs for power, heating, and cooling in both rural and urban regions, off-grid, decentralized, and low-temperature applications will be desirable.”
Read all the Latest News India and Breaking News here
Comments
0 comment