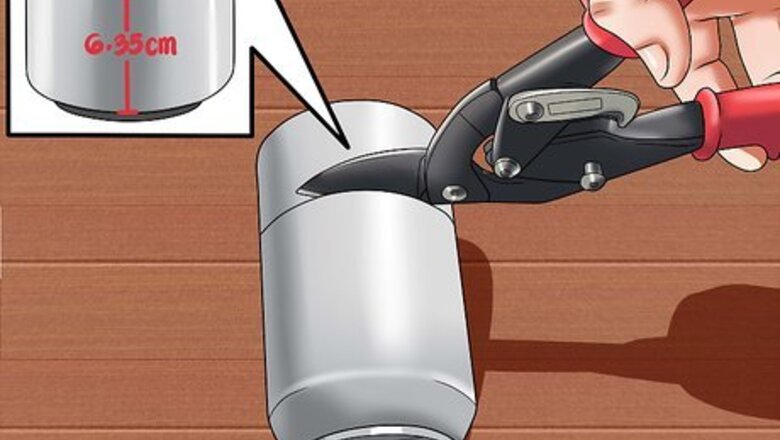
views
Making a Soda Can Steam Engine (For Kids)
Cut an aluminum can to about 2 ⁄2 in (6.4 cm) tall. Use tin snips or shop scissors to make a smooth horizontal cut about 1/3 of the way up from its base and around the can’s circumference.
Fold and crimp the cut rim with pliers. Fold the rim on each piece of the can in on itself to eliminate its sharp edges. Take care not to cut yourself as you do so.
Push the bottom of the can out from the inside to flatten it. Most soda cans have a circular base that curves into the interior of the can. Push this out by flattening it with your fingers or using the bottom of a small glass or jar to smooth it.
Punch two holes on opposite sides of the can ⁄2 in (1.3 cm) from the top. You can use a paper punch for this, or you can make the holes with a nail and hammer. You will need a hole slightly larger than ⁄8 inch (3.2 mm) in diameter.
Place a tea light candle in the center of the can. Crumple foil and place it under and around the candle to hold it in place. Tea light candles come in small tins, so the wax should not melt and spill into your aluminum can.
Wrap the center of a 6–8 in (15–20 cm) long piece of the copper tubing around a pencil 2 or 3 times to make a coil. The ⁄8 inch (3.2 mm) tubing should bend easily around the pencil. You will need enough coiled tubing to stretch across the top of the can, plus about an extra 2 inches (5.1 cm) of straight tubing on each side.
Insert the ends of the tubing through the holes in the can. Center the coil over the wick of the candle. Try to have about the same length of straight tubing sticking out of each side of the can.
Bend the ends of the tube with pliers to make 90-degree angles. Bend the straight sections of the tubing so that they go in opposite directions on each side of the can. Then, bend them again so that they reach below the base of the can. When you're done, you should have a coiled section of tubing in the middle over your candle that stretches downward into two opposite-facing "jets" on either side of the can.
Set the can in a large bowl of room temperature water with the tubing ends submerged. Your "boat" should float comfortably. If the tubing ends don't quite sit below the waterline, try weighing the can down slightly, but be careful not to sink it.
Fill the tubes with water. The easiest way to do this is to place one end in the bowl of water and suck through the other like a straw. Alternately, you can hold your finger over one end and hold the open end under a running faucet.
Light the candle. Over time, the water in the tubing will heat up and begin to boil. As it evaporates into steam, it will shoot out of the "jets" of the tubing, causing the entire can to spin in the bowl.
Making a Paint Can Steam Engine (For Adults)
Cut a rectangular hole near the base of a gallon paint can. Mark a 6 in × 2 in (15.2 cm × 5.1 cm) rectangle horizontally on the side of the can 1 inch (2.5 cm) up from the base. Note that for this paint can (and the other one you'll use), you'll want to ensure that the can contained only latex-based paint and that it has been thoroughly washed with soap and water before use.
Cut a 4 ⁄3 in × 9 ⁄3 in (12 cm × 24 cm) piece of metal mesh. Bend 2 ⁄3 inches (5.9 cm) at either end of the 4 ⁄3 inches (12 cm) side down at a 90-degree angle. This should create a 4 ⁄3 in × 4 ⁄3 in (12 cm × 12 cm) square "platform" with 2 2 ⁄3 in (5.9 cm) "legs". Place this mesh inside the paint can, "legs" down, lining it up with the edges of the hole you cut.
Make a half-circle of holes along the lid's perimeter. Eventually, you'll burn coals inside this paint can to provide the heat for your steam engine. If these coals don't have a steady supply of oxygen, they won't be able to burn well. Allow ventilation by drilling or punching a series of holes in a half-circle pattern along the edge of the can's lid. These ventilation holes should ideally be about ⁄5 inch (1.0 cm) in diameter.
Create a coil from copper tubing. Take about 20 feet (6.1 m) of soft copper tubing ⁄4 inch (0.64 cm) in diameter and measure 1 foot (30 cm) from one end. Starting from this point, wrap the tubing into five coils 5 inches (13 cm) in diameter. Wind the remaining length of the tubing into about 15 coils 3 inches (7.6 cm) in diameter. You should be left with about 8 inches (20 cm) extra.
Run both ends of the coil through the lid ventilation holes. Bend both ends of the coil so that they're pointing upwards and insert each through one of the holes in the lid. If you don't quite have enough length in the tubing, you may need to unwind one of the coils slightly.
Insert the coil and charcoal into the paint can. Place the coil on top of the mesh platform. Fill the space around and inside the coil with charcoal briquettes. Close the lid tightly.
Drill tubing holes in the smaller paint can. In the center of the paint can's lid, drill a hole ⁄5 inch (1.0 cm) in diameter. On the side of the can, drill two ⁄5 inch (1.0 cm) holes - one near the base and one above it near the lid.
Insert corked plastic tubing into the holes on the side of the smaller can. Use the ends of the copper tubing to bore holes in the center of two corks. Insert one 10 inches (25 cm) piece of hard plastic tubing into one cork and one 4 inches (10 cm) piece into the other so that they fit snugly and extend slightly from the other end of the cork. Insert the cork with the longer tubing into the bottom hole on the small can and the cork with the shorter tubing into the top hole. Secure the tubing in each cork with hose clamps.
Connect the larger can's tubing to the smaller can. Place the smaller can above the larger can with the corked tubing facing away from the larger can's ventilation holes. Use metallic tape to secure the tubing from the bottom cork to the tubing extending from the bottom of the copper coil. Then, secure the tubing from the upper cork to the tubing extending from the top of the coil in the same way.
Insert copper tubing through a junction box. Use a hammer and screwdriver to remove the center portion of a circular metallic electrical junction box. Secure an electrical cable clamp to the junction box with the retaining ring inside. Insert 1 6 inches (15 cm) copper pipe with a diameter of ⁄2 inch (1.3 cm) through the cable clamp connector so that the tubing protrudes a few centimeters below the hole in the junction box. Blunt the edges of this end inward with a hammer. Insert this end of the pipe into the hole in the lid of the smaller can.
Insert the skewer into the dowel rod. Take a standard wooden barbecue skewer and insert it into one end of a ⁄5 inch (1.5 cm) hollow wooden dowel rod ⁄8 inch (0.95 cm) in diameter. Place the dowel rod and skewer inside the copper pipe in the metal junction box so that the skewer points up. The skewer and dowel rod will act as the "piston" when the engine is running. To make the motion of the piston easier to see, you might want to attach a small paper "flag" to the top.
Prepare the engine for operation. Remove the junction box assembly from the small upper can and fill the upper can with water, allowing it to drain into the copper coil until the can is about 2/3 full of water. Check all connectors for leaks and ensure all seals are tight. Secure the lids of both cans by tapping them with a hammer. Replace the junction box in its spot above the small upper can.
Run the engine! Crumple up pieces of newspaper and place them in the space enclosed by mesh at the bottom of the engine. When the charcoal has caught fire, allow the briquettes to burn for about 20-30 minutes. As they heat the water in the coil, steam should begin to build up in the upper can. When this steam reaches sufficient pressure, it will push the dowel and skewer piston upwards. Once sufficient pressure has been released, the piston will be pulled back down by gravity. Trim pieces off of the skewer as needed to reduce the weight of the piston - the lighter it is, the more frequently it will "pop" up. Try to whittle the skewer down to a weight such that the piston "runs" at a constant clip. You can speed up the burning process by using a hair dryer to blow through the ventilation holes.
Be safe. It probably goes without saying that this DIY steam engine requires careful handling and operation. Never run the steam engine indoors. Never run it around flammable material like dry leaves or overhanging trees. Only run it on a tough, non-flammable surface like concrete. If you're working with children, ensure an adult is present to supervise at all times. Do not children or teenagers approach the engine while the charcoal is burning. If you're ever not sure how hot the engine is, assume that it's too hot to touch. Also, be sure that the steam is able to escape from the upper "boiler". If the piston becomes stuck for some reason, pressure can build up inside the small can. In a worst case scenario, this can cause the can to explode, which can be very dangerous.
Comments
0 comment