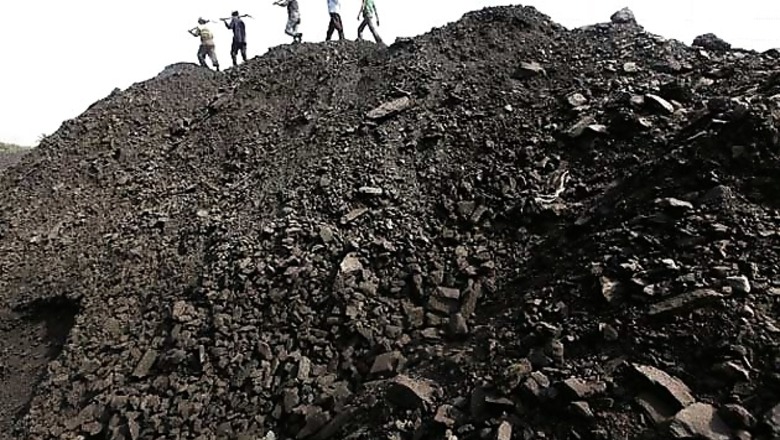
views
For a scientist who is passionate about history, Mark Denys appreciates the importance of the West Bokaro coalfields in the Indian clean coal technology space. It was in these coalfields in Jharkhand that Tata Steel set up the country's first coal washery in 1951. The washery reduced the coal's ash content from as much as 35 per cent to 18 per cent, improving the fuel's efficiency and extending the life of the mines.
More than half a century later, the head of Tata Steel's R&D and Scientific Services realises that the coalfields' next brush with history might well depend on his team. Denys and his colleagues at the company's R&D centre in Jamshedpur are in the advanced stages of developing the next generation of clean coal technology. The new method will further reduce ash content in the West Bokaro coal to 8 per cent, a significant improvement from present standards of about 13-15 per cent. The technology, the first of its kind to be developed by an Indian company, also promises to double the yield of these mines.
Denys realises how much that means for the country's largest steelmaker. Tata Steel already imports half of its coal despite owning mines in West Bokaro and Jharia, also in Jharkhand. "This [the new technology] will decrease our dependency on costly imported coal, reduce our exposure to the coal price market fluctuations and to the dramatic changes in the currency exchange rates like we see today," says Denys, who earlier was in charge of Ironmaking Research at Corus, the British company Tata Steel acquired in 2007.
Not only that. While Tata Steel is increasing its capacity at its century-old Jamshedpur facility, the company also has a massive 6-million-tonne-a-year plant coming up in Orissa that will again push up the need for coal. Black diamond and iron ore are the key raw materials to make steel. And this is where the new technology might help. Says Denys, "With today's best available technology we generate about 35 kg of metallurgical grade coal [used in steelmaking and also called coking coal] for every 100 kg of coal mined…Our new clean coal technology is far more selective. We target to generate about 60 kg of metallurgical grade coal for every 100 kg of coal mined. This means that we nearly double the life of our captive mines!"
The progress in the technology's development has already created a buzz in the industry and a few of Tata Steel's peers in the steel and power sectors have offered to partner. Though the steel company has declined help, it is not hard to see why others would be interested in the technology, for which Tata Steel has already filed 13 patents. India has among the largest reserves of coal in the world at 267 billion tonnes, but most of them have an ash content of up to 35 per cent, compared with the global average of about 15 to 20 per cent. Even with these considerable reserves, many of India's steel and power producers import coal, as the sole producer and supplier in the domestic market, Coal India, has till now failed to ramp up production. This summer has seen rampant power shortages, partly because power plants face coal shortages. Another interesting aspect is that this is one of the first times a chemical process is being used to clean coal in India rather than using the "physical" method of taking ash out of coal. This would involve crushing, grinding, sieving and washing the coal. Its effectiveness, though, is limited and at least 15 per cent of ash still remains in the coal.
"Given India's present and future resource needs, it is very important to have a technology that will make efficient use of resources," says James O'Connell, the Singapore-based managing editor of Platts International Coal Report. Internationally too, miners and end-users of coal in Indonesia, Australia and Japan have, individually or along with partners, made initiatives in improving technology given the finite reserves of the fuel.
But despite the increased research activity globally, there hasn't been a real breakthrough. "The key to a successful technology is that it should be easily replicable and viable. This is where most have failed to deliver," says O'Connell. Denys realises that and reiterates that the Tata Steel management wouldn't have continued to invest in the technology had it not been sure of its viability.
Comments
0 comment