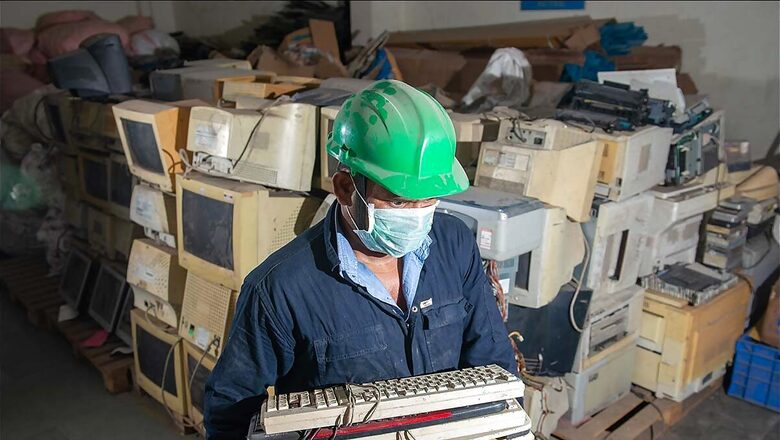
views
Tokyo Olympics used e-waste for medals. India's e-waste laws and extended producer responsibility are in place, but informal processing remains a problem. E-waste awareness programs and cost-effective recycling technologies offer hope for a greener future, addressing environmental and economic challenges.
Electronic waste (e-waste) encompasses discarded items like computer monitors, mobile phones, CDs, TVs, air conditioners, and refrigerators. According to the 2017 Global E-Waste Monitor, India generates approximately 2 million tonnes of e-waste annually, ranking fifth among e-waste producers worldwide, following the US, China, Japan, and Germany.
Shockingly, in 2016-17, India managed only 0.036 million tonnes of its e-waste.
A significant 95% of India’s e-waste is informally and poorly recycled. A United Nations (UN) report from January 24, 2019, highlighted that global e-waste reached 48.5 million tonnes in 2018, with expectations of doubling if action is not taken. Worldwide, only 20% of e-waste is recycled, and poor extraction methods result in a meager 30% recovery rate for essential metals like cobalt, highly demanded in laptops, smartphones, and electric car batteries.
In China, a single recycler already produces more cobalt from recycling than the entire country mines in a year. Recycling metals also proves to be 2 to 10 times more energy-efficient compared to mining virgin ores. To create a more sustainable circular economy, where waste is minimized, resources are conserved, and reused in the supply chain for new products, it is crucial to reduce electronic waste generation and improve end-of-life handling.
A positive example comes from the 2020 Tokyo Olympics, where 50,000 tonnes of e-waste were used to create medals. Organizers collected devices like smartphones and laptops, extracting nearly 8 tonnes of gold, silver, and bronze to produce 5,000 medals, with 90% of municipal authorities in Japan participating in collection efforts.
India has had e-waste management laws in place since 2011, mandating authorized dismantlers and recyclers to handle e-waste. The E-waste (Management) Rules of 2016 expanded its scope to include components, consumables, parts, and spares of Electrical and Electronic Equipment (EEE), strengthening Extended Producer Responsibility (EPR) to ensure the return of end-of-life products.
A new concept called Producer Responsibility Organization (PRO) further enhances EPR. Producers are now required to manage 20% of the waste generated by their sales, with an annual 10% increase for the next five years. Producers are not only responsible for waste collection but also ensuring it reaches authorized recyclers and dismantlers.
Despite these regulations, approximately 80% of e-waste, including laptops, cell phones, cameras, air conditioners, TVs, and LED lamps, continues to be informally processed, posing severe health and environmental risks through groundwater and soil pollution.
India’s e-waste is growing rapidly, with a compound annual growth rate (CAGR) of about 30%. The Associated Chambers of Commerce and Industry of India (ASSOCHAM) estimated e-waste generation at 1.8 million tonnes annually in 2016, projected to reach 5.2 million tonnes per year by 2020.
Efforts are underway to raise awareness about e-waste management. The Ministry of Electronics and Information Technology (MeitY) launched an e-waste awareness program under Digital India in collaboration with industry associations in 2015. This program promotes environmentally friendly e-waste recycling practices, aiming to generate jobs and viable business opportunities locally.
Meity has also developed cost-effective technologies for recycling valuable materials and plastics from e-waste, including two exclusive PCB recycling technologies with acceptable environmental standards. These technologies can be adapted for the informal sector as well.
E-waste contains plastic, making up to 25% of its weight. A process has been developed to convert 76% of this waste plastic into materials suitable for virgin plastic products.
Additionally, micro-factories can transform e-waste into reusable materials for ceramics and plastic filaments for 3D printing, promoting sustainability.
India’s potential for e-waste recycling is immense. While there have been strides in this direction, much remains to be done, including awareness campaigns, skill development, human capital investment, technology adoption, and safety measures in the informal sector.
Given India’s limited mineral resources, a well-designed, robust, and regulated e-waste recovery system could create jobs and wealth while addressing the e-waste challenge.
Comments
0 comment